Table of Contents
Acrylic sheets—often known by the popular name “plexiglass”—have become a staple material in construction, signage, displays, and a multitude of DIY projects. If you are wondering, “how much is a sheet of acrylic?” you are not alone. Whether you’re an architect, a fabricator, or a hobbyist, understanding the cost structure behind acrylic sheets is crucial for budgeting and planning your projects. In this guide, we will explore the ins and outs of acrylic sheet pricing, compare it with other materials, break down the factors that influence cost, and offer actionable tips to get the best value for your investment.
In the following sections, we’ll explain what acrylic sheets are and why they are favored over traditional glass, discuss the key variables that affect pricing, provide a detailed breakdown of costs based on dimensions and thickness, and examine how supplier differences and regional factors play into the final price. Finally, we answer common questions that many buyers ask about acrylic sheet costs.
Whether you are shopping for a single sheet for a custom project or buying in bulk for a commercial installation, this article will serve as your definitive resource on acrylic sheet pricing. By the end, you will have a clear understanding of how much a sheet of acrylic costs, what drives that cost, and how you can ensure you get the best deal without sacrificing quality.
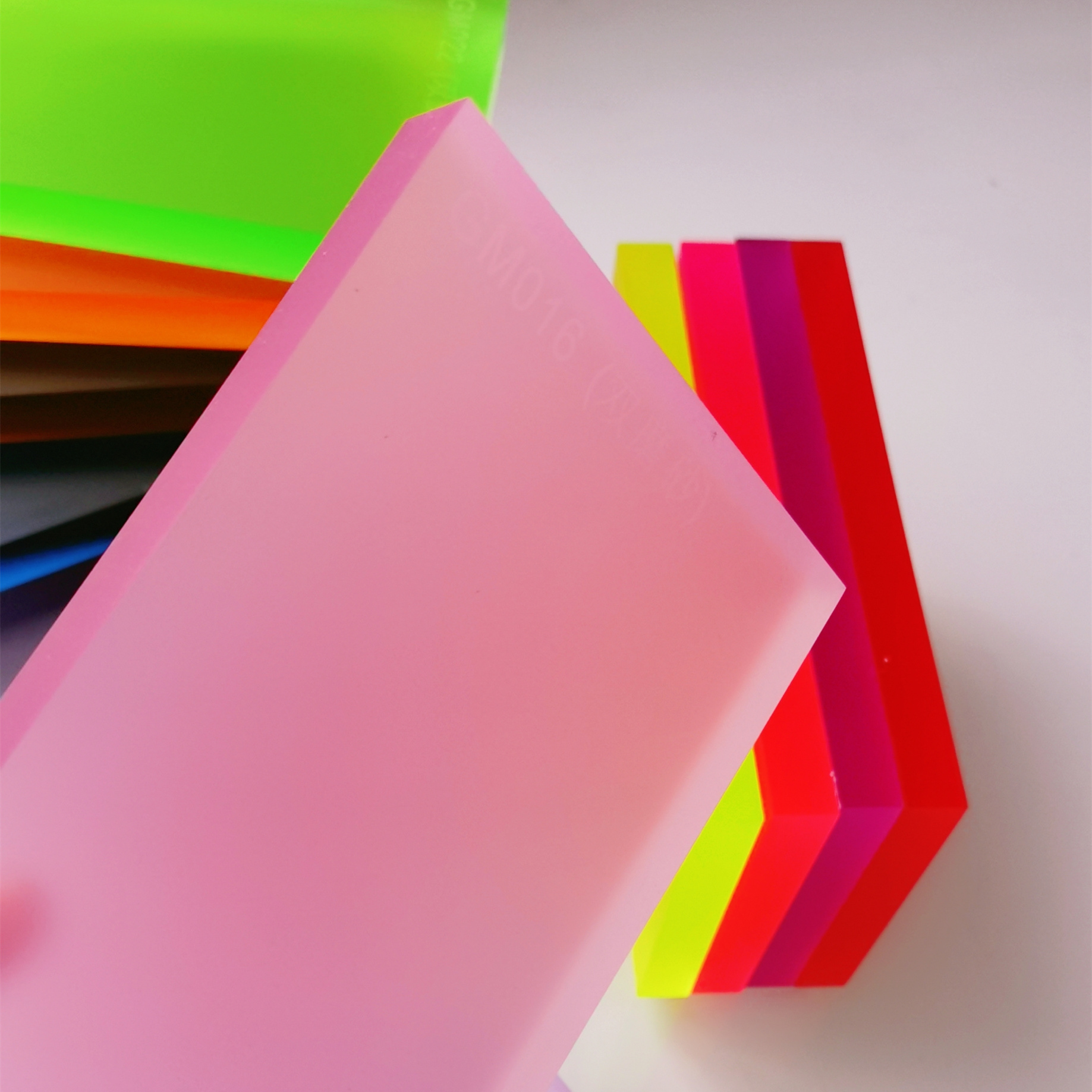
1. Overview of Acrylic Sheets
What Are Acrylic Sheets?
Acrylic sheets are a type of transparent thermoplastic derived from polymethyl methacrylate (PMMA). Known for their glass-like clarity, lightweight nature, and high impact resistance, acrylic sheets offer many advantages over traditional glass. They are commonly used as windows, skylights, displays, and protective barriers (often referred to as sneeze guards). The material is available in various forms, including extruded and cast acrylic, each with distinct physical properties and price points.Properties and Applications
Acrylic sheets are renowned for several properties that make them ideal for a wide range of applications:- Optical Clarity: They are exceptionally clear and can even outperform glass in optical clarity, especially in thicker sections.
- Impact Resistance: Acrylic is much more resistant to impact than glass, making it a safer option in applications where breakage could pose a risk.
- Lightweight: It weighs about half as much as glass, reducing transportation and installation costs.
- UV Resistance: Many acrylic sheets offer good UV resistance, which minimizes yellowing and maintains clarity over time.
- Versatility: Easily cut, drilled, and thermoformed, acrylic sheets can be adapted for a vast range of applications, from DIY crafts to high-end architectural projects.
Extruded Versus Cast Acrylic
The two primary types of acrylic sheets are extruded and cast:- Extruded Acrylic: Manufactured by pushing molten acrylic through a die, these sheets tend to be more cost-effective and have a consistent thickness, though they may offer slightly lower optical quality.
- Cast Acrylic: Produced by pouring liquid acrylic into a mold, cast acrylic typically has superior optical clarity and higher impact strength, albeit at a higher price.
2. Factors Affecting the Cost of Acrylic Sheets
Thickness and Dimensions
The physical dimensions and thickness of an acrylic sheet are among the most significant factors affecting its cost:- Thickness: Acrylic sheets range from as thin as 1/16 inch (approximately 1.5 mm) to several inches thick. Thicker sheets, such as 1/4 inch or 3/8 inch, are more expensive due to higher raw material use and more complex processing. For instance, a standard 4′ × 8′ sheet of 1/8-inch acrylic can average around $100.
- Size: Larger sheets cost more in total because they cover a greater area. Prices are often quoted per square foot or square meter, so calculating the total area helps in comparing costs across suppliers.
Type of Acrylic: Extruded vs. Cast
The manufacturing method is a key price determinant:- Extruded Acrylic: Typically less expensive due to a streamlined production process and is used when high optical quality is not critical.
- Cast Acrylic: Offers superior clarity and durability, making it ideal for premium applications, but it comes at a higher cost.
Finishes and Colors
Acrylic sheets are available in clear, tinted, frosted, mirrored, and colored variants, and each option influences the cost:- Clear Acrylic: Standard clear sheets are usually the baseline for pricing.
- Colored or Tinted Acrylic: These options can be slightly more expensive due to added pigments and processing requirements.
- Special Finishes: Additional features such as anti-glare or UV protection coatings further increase the price.
Supplier and Brand Differences
Pricing can vary based on supplier and brand:- Quality Assurance: Established brands known for consistent quality, like Plaskolite or Professional Plastics, may charge a premium.
- Volume Discounts: Bulk orders often receive discounts, which is beneficial for commercial projects.
- Geographic Location: Regional factors and shipping logistics can cause price differences between domestic and international suppliers.
Customization and Processing
Additional services can add to the cost:- Cut-to-Size Services: Custom cutting may incur a fee, but it can reduce waste and save time.
- Additional Fabrication: Processes like thermoforming, polishing, or CNC routing further influence the final cost.
3. Price Comparisons: Acrylic Versus Other Materials
Glass
- Price: A 4′ × 8′ sheet of 1/8-inch glass may cost around $200, roughly twice the price of acrylic.
- Weight and Durability: Glass is heavier and more fragile, increasing transportation and installation costs.
- Application Suitability: While glass offers superior scratch resistance and ease of cleaning, acrylic’s impact resistance and light weight make it more suitable for many safety applications.
Polycarbonate
- Price: Polycarbonate sheets are similarly priced to acrylic, with a 4′ × 8′ sheet of 1/8-inch polycarbonate also around $100.
- Durability: Although polycarbonate is tougher and more impact resistant, it may be more prone to scratching and can yellow over time under UV exposure.
- Choosing Between Them: Acrylic is often preferred when optical clarity and scratch resistance are priorities.
PVC Foam Board
- Price: A 4′ × 8′ sheet of 1/2-inch PVC foam board can cost around $50.
- Durability and Applications: PVC foam board is lightweight and economical, but it lacks the clarity and durability of acrylic, making it more suited for temporary or non-critical applications.
- Cost Trade-Offs: While cheaper, PVC foam board may not be ideal for projects requiring long-term durability or high optical quality.
4. Detailed Pricing Breakdown by Thickness and Size
Typical Price Ranges for a 4′ × 8′ Sheet
- 1/16 inch (≈1.5 mm, Extruded): $40 – $60
- 1/8 inch (≈3 mm, Extruded): $80 – $120
- 1/8 inch (≈3 mm, Cast): $100 – $150
- 1/4 inch (≈6 mm, Extruded): $150 – $250
- 1/4 inch (≈6 mm, Cast): $200 – $300
- 3/8 inch (≈9 mm, Cast): $250 – $400
Cost per Square Foot
Many suppliers price acrylic sheets per square foot. For instance:- 1/8 inch extruded acrylic: Approximately $2.00 to $2.50 per square foot.
- Cast acrylic: Typically slightly higher due to enhanced optical quality.
Variations with Custom Sizes and Finishes
Prices can fluctuate when custom sizes or special finishes are required:- Custom Cuts: May incur additional fees per sheet.
- Special Finishes: Coatings such as UV protection or anti-glare can add 10% to 50% on top of the base price.
5. How to Calculate Your Acrylic Sheet Cost
Step-by-Step Cost Calculation
- Calculate the Area: Multiply the width by the length (e.g., 4′ × 8′ = 32 square feet).
- Determine the Price Per Square Foot: Multiply the area by the supplier’s unit cost (e.g., 32 sq ft × $2.50 = $80.00).
- Add Customization Fees: Include any additional fees for cutting or finishing (e.g., $20 per sheet).
- Consider Bulk Discounts: Apply any discounts for large orders.
- Include Shipping and Handling: Factor in any delivery fees.
- Base Material Cost per sheet: 32 sq ft × $2.50 = $80.00
- Customization Fee per sheet: $15.00
- Total per Sheet Before Discount: $80.00 + $15.00 = $95.00
- After 10% Discount: $95.00 × 0.90 = $85.50 per sheet
- Total for Three Sheets: 3 × $85.50 = $256.50
6. Tips for Buying Acrylic Sheets at the Best Price
Comparing Suppliers and Ordering in Bulk
- Research Online: Compare supplier reviews, quotes, and product specifications from reputable sources such as Acme Plastics, Shapes Plastics, and Professional Plastics.
- Request Quotes: Contact suppliers directly for bulk orders or custom specifications to secure competitive pricing.
Choosing the Right Type and Finishes
- Select the Appropriate Type: Determine if extruded acrylic meets your needs or if cast acrylic’s enhanced clarity justifies the extra cost.
- Stick to Standard Finishes: Avoid additional coating fees if they are not necessary for your application.
Optimizing Dimensions and Considering Additional Costs
- Standard Sizes: Standard 4′ × 8′ sheets are generally more cost-effective than custom dimensions.
- Efficient Material Use: Plan your project layout to minimize waste.
- Factor in Shipping and Processing Fees: Always include these in your overall cost calculations.
7. Future Trends and Market Considerations
Technological Advancements
- Innovations in production may lower costs over time.
- Advances in cutting and fabrication technology can reduce custom processing fees.
Market Demand and Supply Chain Factors
- Growing demand in home improvement and commercial signage can lead to price fluctuations.
- Global supply chain disruptions and raw material cost changes can temporarily affect pricing.
Sustainability and Economic Conditions
- Recycled acrylic sheets may become more common as sustainable practices evolve.
- Regional economic conditions and bulk purchasing trends can impact overall pricing and availability.